Education & Training
Cleaver-Brooks offers online, custom on-site, or classroom education and training for engineers, maintenance personnel and operators. Keep up with industry best practices and stay current on certifications with technology-based solutions to real-world challenges.
Have a question or want more information? Email us at CBacademy@cleaverbrooks.com
Upcoming Events
Hydronics On-Site Training - Request a Quote Now!
This course is designed for facilities that operate boilers from our ClearFire Family of products. It is also intended for contractors and our Manufacturer’s Rep Network that maintain or manage facilities utilizing ClearFire boilers.
On-Site Training - Request a Quote
Our on-site training covers all boiler types regardless of manufacturer. System training for steam or hot water can also be included. After learning more about your personal objectives, who from your facility will be attending the training, the levels of experience of each attendee, and the equipment involved, we’ll create a tailored agenda to ensure the training session meets your needs.
Boiler Operation / Electrical Troubleshooting Course - Register Now!
This two-day in-person educational training is targeted specifically for our end user customers looking to gain the fundamental concepts of boilers, boiler controls, proper operation, and electrical troubleshooting.
Boiler Room Essentials Online Course Sign up Today!
Boiler Room Essentials is an online, self-paced learning course designed to educate individuals that are looking for a career in the steam boiler operations field or just gain an understanding of the high pressure steam boiler industry. The course is geared for various levels of knowledge bases; whether you are just starting out, or you have been in the industry for many years this course is for you.
Boiler Room Essentials Textbook ONLY
High Pressure Boilers provides a comprehensive overview of the safe and efficient operation of high pressure boilers and related equipment. The latest combustion control technology, as well as EPA regulations and their implications, are included in this edition
%20680x330.jpg)
%20680x330.jpg)
%20680x330.jpg)
Training Events & Webinars
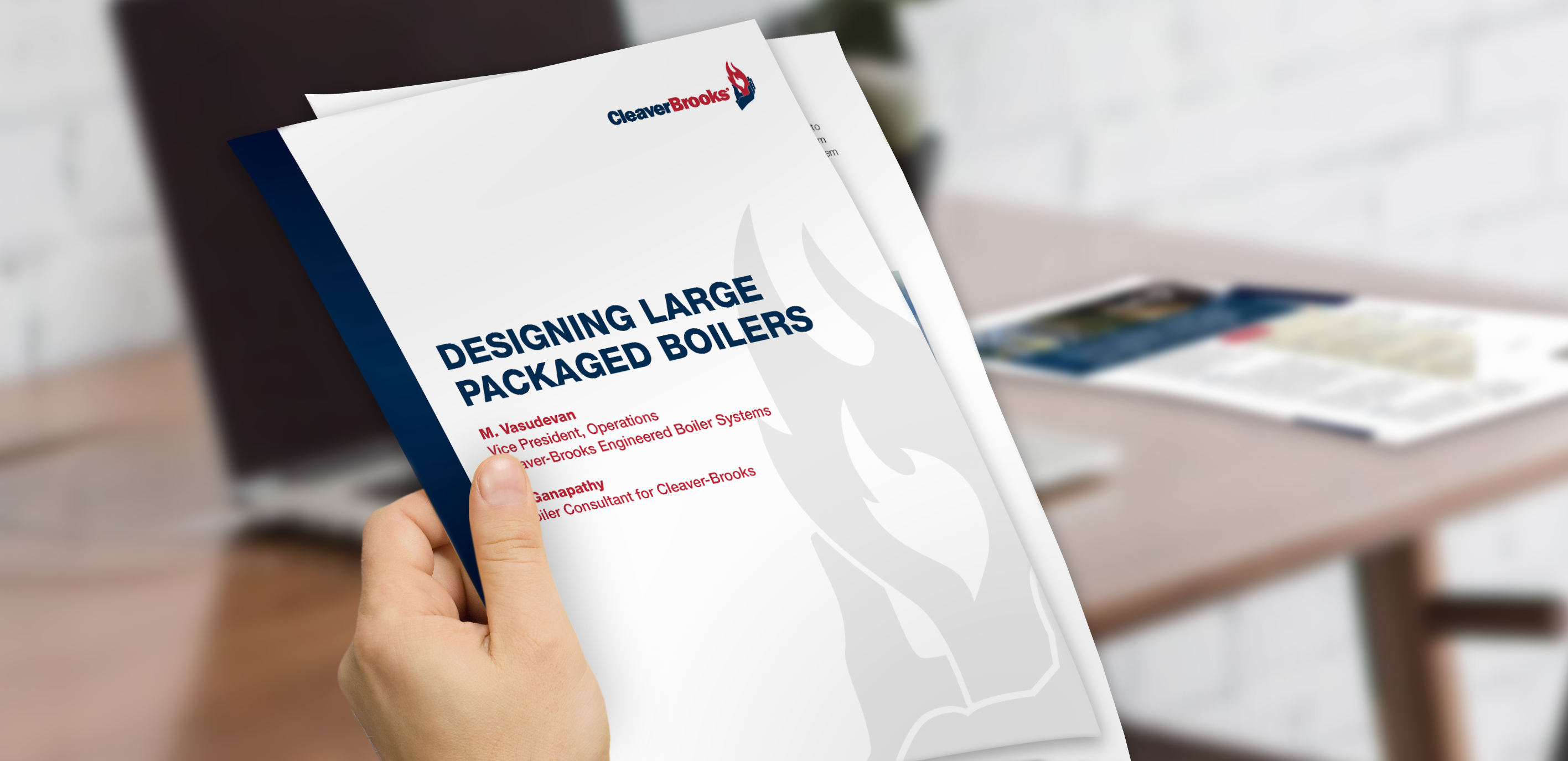
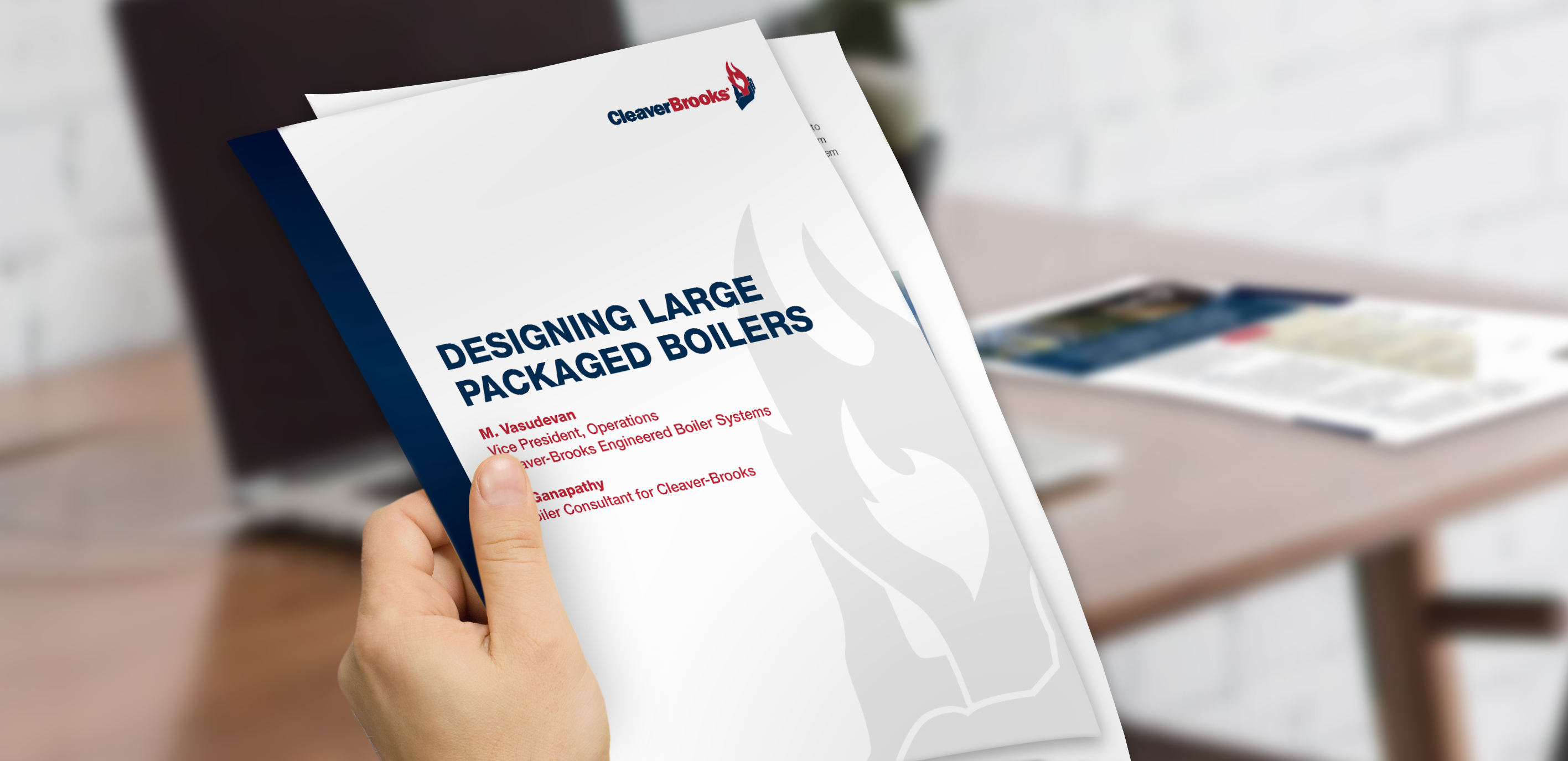
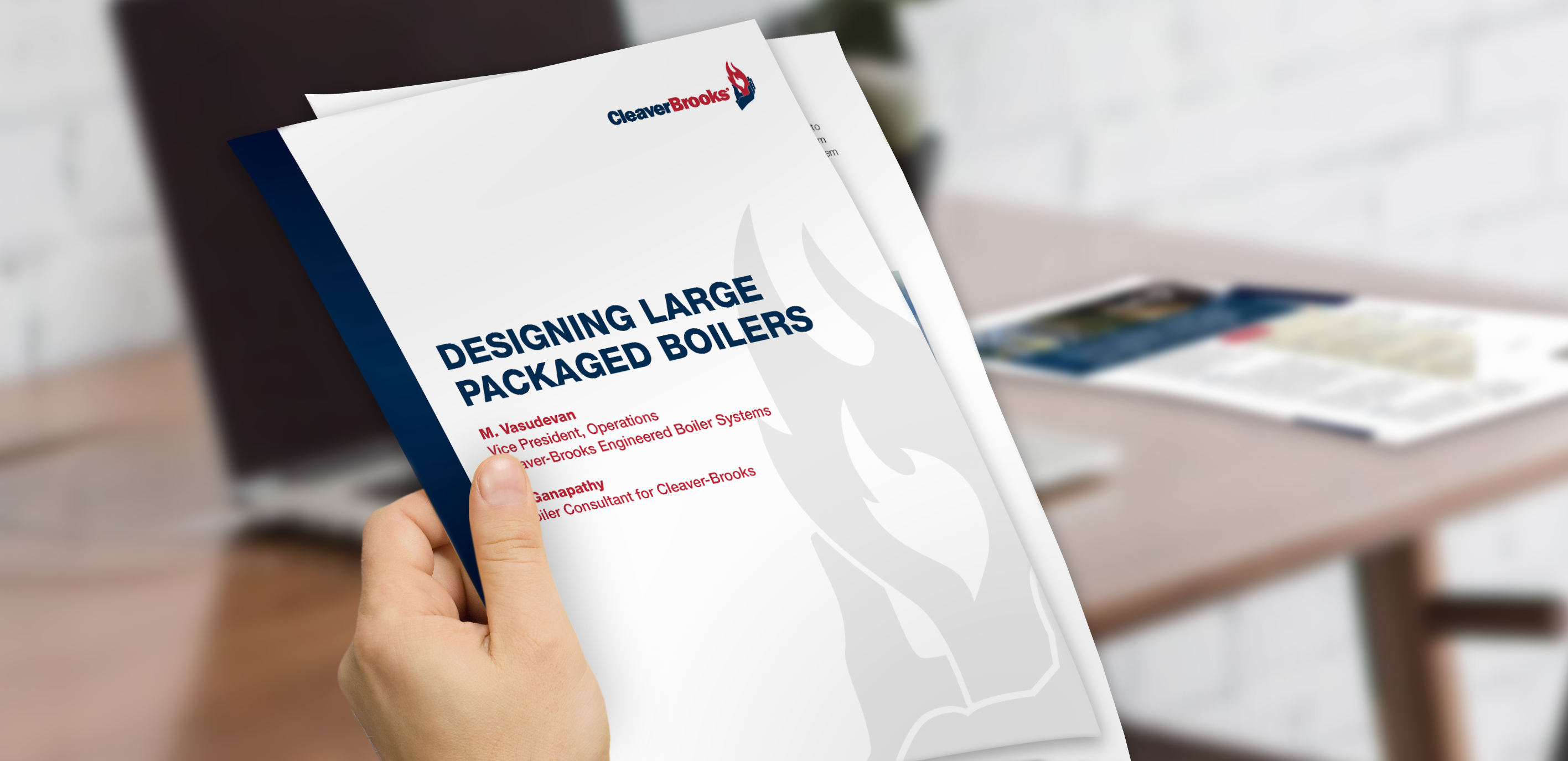